Top UK Fiber Laser: Unveiling the Advancements and Potential of Laser Technology
By:Admin
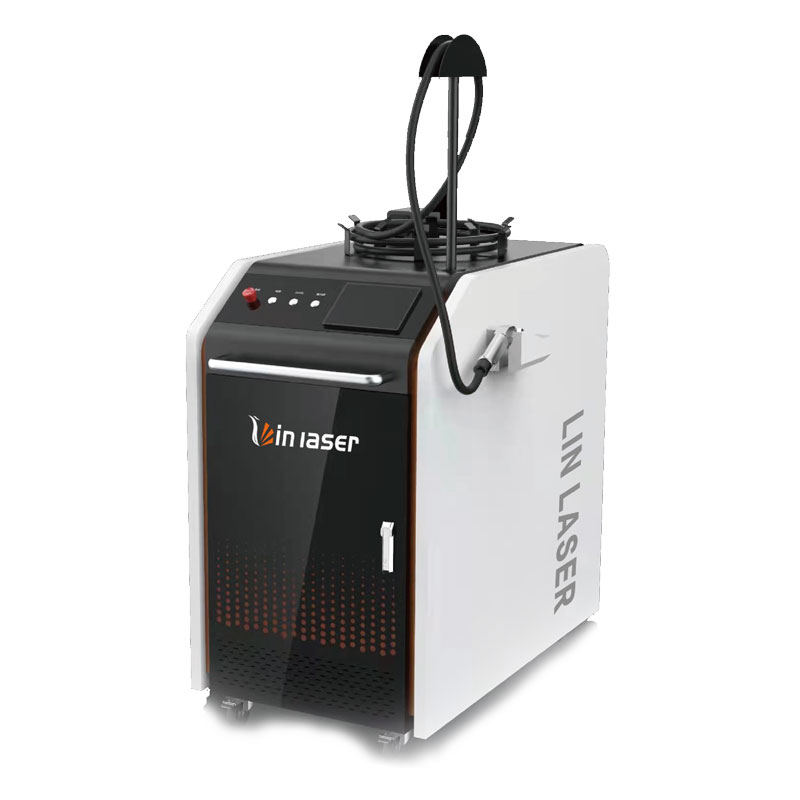
Introduction:
In the realm of laser technology, Fiber Laser UK (brand name to be removed) has emerged as a leading innovator, revolutionizing multiple industries with its cutting-edge fiber laser solutions. With a commitment to research and development, the company has consistently pushed the boundaries of what is possible, cementing its position as a trailblazer in the field. This news article explores the latest breakthroughs in fiber laser technology and their potential impact on various sectors.
1. The Rise of Fiber Laser Technology:
Fiber laser technology has witnessed significant growth in recent years, offering unparalleled advantages over traditional laser solutions. These solid-state lasers harness the amplified light generated through optical fibers, resulting in superior energy efficiency, increased beam quality, and higher power output. Compared to gas and crystal-based lasers, fiber lasers exhibit longer operational lifespans and require minimal maintenance, making them more cost-effective in the long run.
2. Applications in Manufacturing and Industrial Sectors:
Fiber lasers have made substantial inroads into the manufacturing and industrial sectors, facilitating precise and efficient material processing. With their exceptional cutting and welding capabilities, fiber lasers are rapidly replacing conventional cutting methods. The high-power output of fiber lasers enables enhanced productivity, reduced downtime, and improved precision, offering a competitive edge to industries dealing with metal fabrication, automotive manufacturing, aerospace, and more.
3. Medical Advancements Enabled by Fiber Laser Technology:
The medical field has experienced remarkable advancements owing to fiber laser technology. Laser-based surgical procedures, such as laser eye surgeries and dermatological treatments, have become more reliable and precise with the introduction of fiber lasers. These lasers are highly controllable, enabling surgeons to precisely target specific tissues with minimal damage to surrounding areas. Moreover, fiber lasers are also being used in medical research, aiding in the development of diagnostic tools and therapies.
4. Impact on Telecommunications and Information Technology:
Fiber laser technology has transformed the telecommunication and information technology sectors, primarily through advancements in fiber-optic communications. By utilizing fiber lasers for data transmission, telecommunication networks can transmit data over long distances at higher speeds, resulting in faster internet connections and improved voice and video call quality. Additionally, fiber lasers have facilitated the development of compact and efficient optical amplifiers and fiber optic sensors, enhancing network performance and reliability.
5. Sustainable and Environmentally Friendly Solutions:
As sustainability becomes an increasingly important consideration across industries, fiber lasers offer an eco-friendly alternative. Fiber lasers have a lower environmental impact compared to their counterparts, such as carbon dioxide lasers, as they consume less power and generate minimal waste. The energy efficiency of fiber lasers contributes to reducing carbon footprints while maintaining optimal performance, making them an attractive choice for environmentally conscious businesses.
Conclusion:
Fiber Laser UK (brand name to be removed) has revolutionized various sectors with its cutting-edge fiber laser technology. From manufacturing and medical applications to telecommunication advancements, fiber lasers have become a game-changer in multiple industries. With their unparalleled efficiency, superior beam quality, and versatility, fiber lasers are poised to drive further innovation and progress. As technology continues to evolve, it is crucial to keep an eye on Fiber Laser UK to witness the next wave of advancements in this field.
Company News & Blog
Minimizing Laser Cutting Focus Shift with New Algorithm and Non-Contact Beam Measurement Platform
Messer Cutting Systems, a leading company in the manufacturing and supply of high-quality cutting-edge technologies and systems for various industries, has recently introduced a new algorithm that has the capability of reducing the focus shift in laser cutting systems to a minimum. This advanced technology coupled with a new noncontact beam measurement platform has been developed using the most up-to-date fiber laser technology.The company's new algorithm has been designed to reduce the focus shift produced in a laser cutting process. The focus shift created in the process is the result of thermal changes. Thermal changes cause a shift in the focus point of a laser beam and this ultimately leads to poor quality cuts. The shift in the laser focal point can have an impact on the quality and quantity of cuts made, thus making it a critical challenge in the laser cutting industry.To address this challenge, Messer Cutting Systems has introduced an advanced noncontact beam measurement system that integrates seamlessly with the existing fiber laser technologies. This new measurement system has been designed to measure the beam power, beam quality, and beam position, thus providing a complete overview about the current status of the laser beam. The new noncontact beam measurement platform helps to monitor and correct the focus shift in the laser cutting machines, which is designed to offer exceptional precision and accuracy in the cutting process.Messer Cutting Systems is known for its continuous innovations and research and development in the industry. The company has an experienced team of engineers and scientists, who are experts in their respective fields, to meet the needs and requirements of their customers. This has enabled the company to develop and produce high-quality laser cutting systems that are specifically engineered to meet the precise needs of their clients.In addition, the company has also introduced another innovative technology that sets it apart from the conventional laser cutting systems. The new technology is a "smart" cutting technology that reduces the operating costs involved in the laser cutting process. The system can cut down on the amount of wasted material and reduce energy costs, resulting in lower production costs and enhanced production efficiency. The intelligent technology uses sensors and cameras to scan the material, and then optimizes the cutting patterns based on the material characteristics.Messer Cutting Systems is committed to providing a complete range of laser cutting solutions in various industries, including automotive, defense, aerospace, energy, and more. With state-of-the-art technology and advanced laser cutting systems, the company is poised for growth and is highly focused on continually developing new and innovative technologies that push the boundaries of the laser cutting industry.In conclusion, Messer Cutting Systems is an innovative and visionary company that is at the forefront of the laser cutting industry. The company has introduced advanced technologies that not only address the challenges faced by the industry but also provide smart solutions that enable higher productivity, better quality, and lower costs. With its continued dedication to innovation and customer satisfaction, Messer Cutting Systems is poised for future growth and success.
Advanced CO2 Laser for Woodworking Applications: Automatic Focusing, Adjustable Table, Rotary Attachment, and Enhanced Durability
A Powerful Tool for Precision and Versatility: The CO2 Laser TableIn today's ever-evolving woodworking industry, having the right tools at your disposal is crucial to stay ahead of the competition. One such tool that has revolutionized the woodworking process is the CO2 laser table. This ingenious piece of equipment combines precision, versatility, and efficiency to enhance your woodworking capabilities like never before.One of the standout features of the CO2 laser table is its automatic focusing mechanism. This allows for quick and precise adjustments, ensuring that your laser beam is always focused on the desired area. In the past, manually focusing the laser beam could be time-consuming and often resulted in less than perfect outcomes. With the automatic focusing feature, you can now save time and achieve impeccable precision in your woodworking projects.Another remarkable aspect of the CO2 laser table is its automatically adjustable working table. Unlike traditional woodworking tables that are static and limited in their adaptability, the CO2 laser table can accommodate odd-shaped stock effortlessly. This means you can work on a wide variety of materials with different shapes and sizes, expanding your creative possibilities and making it easier to bring your vision to life.To further enhance its versatility, the CO2 laser table comes with a rotary attachment. This attachment allows you to work on cylindrical objects such as mugs, vases, and even wine glasses. With this feature, you can add intricate designs, logos, or even personalized engravings to give your work a unique touch.One of the most essential components of the CO2 laser table is the laser tube itself. (Brand name) utilizes top-of-the-line RECI laser tubes, renowned for their durability and power. These tubes ensure consistent and efficient performance, allowing for crisp and clean cuts or engravings on various materials. Whether you're working with wood, acrylic, leather, or even fabric, the CO2 laser table's laser tube will deliver impeccable results every time.The CO2 laser table is not only equipped with advanced laser technology but also designed for durability and stability. The HG series linear rails incorporated into the design provide high load capacity and rigidity. This ensures smooth and precise movements, even when working on large or heavy projects. No longer will you have to worry about inaccuracies or unsteady surfaces affecting the quality of your work.With a lifting height of 12 inches, the CO2 laser table caters to woodworking projects of varying sizes and requirements. Whether you're engraving intricate designs on a delicate piece or cutting through thick wood with utmost precision, this machine has got you covered. The generous lifting capacity paired with the automatic focusing and adjustable working table features make the CO2 laser table a highly versatile tool that can tackle a wide range of woodworking tasks.In conclusion, the CO2 laser table is a game-changer in the woodworking industry. With its automatic focusing mechanism, adjustable working table, and the ability to accommodate odd-shaped stock, it offers unparalleled precision and versatility. The rotary attachment allows for working on cylindrical objects, expanding your possibilities even further. With (brand name)'s choice of premium materials such as RECI laser tubes and the HG series linear rails, this machine delivers consistent and reliable performance. Whether you're a professional woodworker or an enthusiastic hobbyist, the CO2 laser table is the perfect companion to take your woodworking skills to the next level.Keywords: CO2 laser table, woodworking, automatic focusing, adjustable working table, precision, versatility, rotary attachment, power, durability, RECI laser tubes, HG series linear rails, lifting height.
Revolutionary Laser Tube Cutting Machine Unveiled in Latest News Content
Title: Revolutionary CNC Laser Tube Cutting Machine Enhances Precision and Efficiency in Industrial ManufacturingIntroduction:In the ever-evolving realm of industrial manufacturing, a groundbreaking innovation has emerged. The advent of CNC (Computer Numerical Control) technology has revolutionized the way components are manufactured, offering unmatched precision and efficiency. One such remarkable CNC machine, the Laser Tube Cutting Machine, is poised to make waves in the industry by providing unparalleled cutting accuracy and versatility. Overview of CNC Laser Tube Cutting Machine:The CNC Laser Tube Cutting Machine represents the apex of manufacturing technology, offering a comprehensive solution for shaping and cutting tubes with uncompromising precision. This cutting-edge machine is equipped with advanced laser technology, controlled by a master computer via a software interface. Its ability to operate autonomously ensures optimal performance and seamless integration into existing manufacturing processes.Precision and Accuracy:The CNC Laser Tube Cutting Machine boasts an outstanding level of precision and accuracy in creating intricate designs across a wide range of materials, including metal, plastic, and composite materials. With laser-guided technology, the machine guarantees consistent perfection, eliminating any human errors that may arise during the traditional cutting process. This precision enables manufacturers to achieve exact specifications while minimizing material waste, reducing costs, and enhancing overall product quality.Versatility and Adaptability:Versatility is a key strength of the CNC Laser Tube Cutting Machine. The machine possesses the ability to cut tubes of various shapes, sizes, and thicknesses, ensuring that it meets the specific requirements of diverse manufacturing projects. The flexibility to work with multiple materials and tube profiles enhances the machine's adaptability, making it an indispensable tool in various industries, including automotive, aerospace, construction, and beyond.Efficiency and Time-Saving:The CNC Laser Tube Cutting Machine streamlines the manufacturing process by significantly reducing production time, which results in improved efficiency and cost-effectiveness. The machine's high-speed laser cutting technology enables manufacturers to swiftly and accurately complete even the most complex tube cutting tasks. By automating the process, the machine minimizes production bottlenecks, allowing manufacturers to meet strict deadlines and increasing overall production capacity.Safety Features:Prioritizing the safety of operators, the CNC Laser Tube Cutting Machine comes equipped with cutting-edge safety features. The machine includes sensor systems that detect any unexpected obstructions or malfunctions, immediately halting the cutting process to prevent accidents and protect the operator's well-being. These safety measures ensure peace of mind and maintain uninterrupted workflow throughout the manufacturing process.Future Possibilities:As the CNC Laser Tube Cutting Machine continues to enhance its capabilities and adaptability, the future prospect for industrial manufacturing looks increasingly promising. The machine's constant evolution promises to overcome current limitations by incorporating advancements such as artificial intelligence and machine learning algorithms. These enhancements propel the industry into the era of smart manufacturing, steadily improving production efficiency and establishing new standards of excellence.Conclusion:The advent of the CNC Laser Tube Cutting Machine heralds a new era in industrial manufacturing, revolutionizing the way components are produced. With its unmatched precision, adaptability, and efficiency, this groundbreaking technology is set to reshape the industry and open doors to limitless possibilities. As more manufacturers embrace this innovative tool, the CNC Laser Tube Cutting Machine will undoubtedly become an indispensable asset, transforming industrial manufacturing processes for years to come.
Differentiating Welding Categories: A Comprehensive Guide
Welding Categories: A Comprehensive GuideWelding is a process of joining two or more metal pieces together by melting and fusing them. It is an essential part of the manufacturing process in various industries such as construction, automotive, aerospace, and many more. There are various welding categories, each with its own set of benefits and limitations. In this article, we will provide a comprehensive guide to the different welding techniques.Shielded Metal Arc Welding (SMAW)Shielded Metal Arc Welding, also known as stick welding, is a commonly used welding technique that uses a consumable electrode, which is coated with a flux to protect the weld from contamination. The process involves striking an arc between the electrode and the metal pieces, which melts the metal and fuses it together. SMAW is versatile and can be used for welding both ferrous and non-ferrous metals. It is ideal for outdoor welding as it is not affected by wind or rain.Gas Tungsten Arc Welding (GTAW)Gas Tungsten Arc Welding, also known as Tungsten Inert Gas Welding (TIG welding), is a welding technique that uses a non-consumable tungsten electrode to produce the weld. A shielding gas such as argon is used to protect the weld from contamination. GTAW is commonly used for welding thin sections of stainless steel and non-ferrous metals such as aluminum, magnesium, and titanium. It produces a clean and precise weld, making it ideal for welding in the aerospace and medical industries.Gas Metal Arc Welding (GMAW)Gas Metal Arc Welding, also known as Metal Inert Gas Welding (MIG welding), is a welding technique that uses a consumable wire electrode to produce the weld. A shielding gas such as argon and carbon dioxide is used to protect the weld from contamination. GMAW is commonly used for welding ferrous and non-ferrous metals, such as steel, aluminum, and copper. It is a simple and cost-effective welding process that produces high-quality welds.Flux-Cored Arc Welding (FCAW)Flux-Cored Arc Welding is a welding process that uses a consumable tubular electrode with a flux core. The flux core generates a shielding gas that protects the weld from contamination. FCAW is similar to GMAW, but it is more suitable for welding thicker sections of metal. It is commonly used in the construction and shipbuilding industries.Plasma Arc Welding (PAW)Plasma Arc Welding is a welding process that uses a high-velocity plasma arc to melt the metal and fuse it together. A shielding gas such as argon is used to protect the weld from contamination. PAW is commonly used for welding thin sections of metal and for precision welding in the aerospace and medical industries. It produces a precise and uniform weld with minimal distortion.Oxy-Fuel Welding (OFW)Oxy-Fuel Welding is a welding process that uses a flame generated by mixing oxygen and a fuel gas, such as acetylene, to melt the metal and fuse it together. OFW is commonly used for welding ferrous metals such as steel and cast iron. It is a versatile welding process, but it requires a high level of skill and experience to produce high-quality welds.ConclusionIn conclusion, welding is an essential part of the manufacturing process in various industries. There are various welding categories, each with its own set of benefits and limitations. The choice of welding technique depends on the type of metal being welded, the thickness of the metal, and the desired outcome. Companies like {} are dedicated to providing high-quality welding products and services to meet the needs of the industry. As technology continues to evolve, we can expect to see new welding techniques being developed to improve the efficiency and quality of welding.
Tips to Avoid Machine Cutting Errors in Woodworking
Cutting machines have become an essential tool in the manufacturing industry, allowing businesses to cut materials quickly and efficiently. One popular cutting machine is the 1015 machine, which is known for its high precision cuts and versatility. However, even the most skilled operators can encounter problems when using a cutting machine, which can result in failed cuts or damages to the equipment.In this blog, we will discuss common mistakes that operators make when using a cutting machine, how to prevent them, and how to optimize your machine for maximum results.Mistake #1: Incorrect Material SetupOne of the most common mistakes that operators make when using a cutting machine like the 1015 is not setting up the material correctly. It might sound like a simple thing to do, but even a small mistake can cause significant problems. For example, if you don't adjust the material to the machine's specifications, you might end up with uneven or jagged cuts. This can lead to wasted materials and additional time and expenses to fix the errors.To prevent this from happening, make sure you read the manual and familiarize yourself with the machine's specifications. Next, ensure that you have the right tools and clamps to keep the materials securely in place. Finally, double-check the setup before you start cutting to ensure that everything is in the right place.Mistake #2: Using the Wrong BladeAnother common mistake is using the wrong blade for the materials you're cutting. For example, if you're cutting metal, you need a different blade than if you're cutting wood. Using the wrong blade can lead to dullness, chipping, and eventually damage to the machine itself.Before you start cutting, make sure that you have the right blade for the job. Research the blade types, sizes, and thicknesses suitable for the material you're cutting. Ensure that the blade is properly set up and lubricated for smooth and clean cuts.Mistake #3: Insufficient MaintenanceCutting machines require regular maintenance to keep them running at their best. However, many operators neglect this important step, which can cause several problems. For example, unchecked debris can build up and jam the machine, resulting in damage or subpar cuts.To prevent this, make sure that you have a maintenance schedule in place and follow it diligently. Regularly check for debris like sawdust or metal filings and clean the machine's mechanisms. Ensure that all the components are well lubricated and adjust any components that might have shifted or become loose.Mistake #4: Operator ErrorSometimes, the mistakes made when using a cutting machine are not related to the machine itself. Instead, operator error can cause damage, improper cuts, or wasted materials.To prevent this, make sure that you or your operators are well-informed and adequately trained in how to use the machine. Always keep safety in mind and wear protective equipment, such as goggles and gloves. Finally, ensure that the operator is focused and not distracted when using the machine.ConclusionThe Oliver Machinery 1015 Cutting Machine is an excellent tool for businesses looking to increase their efficiency and precision. However, ensuring the machine continues to perform at its best requires careful attention and maintenance. By avoiding common mistakes like incorrect material setups, using the wrong blades, insufficient maintenance, and operator error, you can ensure that your cutting machine works efficiently and delivers optimum results.In summary, whenever you experience problems with a cutting machine, take your time, review the above points, and make any necessary adjustments. Applying these best practices will help you optimize your cutting machine, extend its lifespan, and enjoy the benefits of increased efficiency and profitability in your business.
Discover the Benefits of Fiber and CO2 Laser Technology for Your Business
In today's world, manufacturing businesses face a range of challenges. From cost pressures to competitive environments, modern firms must remain up-to-date with the latest technological developments to thrive and survive. One of the key innovations of recent years that is changing the world of manufacturing is laser technology.Lasers offer businesses a range of advantages over traditional manufacturing methods. They are precise, fast, and can be easily automated. Laser technology can be used for cutting, drilling, welding, and marking, making it an incredibly versatile tool.Two types of lasers are commonly used in the manufacturing industry: fiber and CO2 lasers. Both have their unique advantages and are suited to different applications.CO2 lasers are better suited to cutting and engraving materials such as wood, acrylic, and plastics. Fiber lasers, on the other hand, are ideal for metal cutting and welding applications. Both types of lasers are widely used across a range of industries such as automotive, electronics, and aerospace. The integration of laser cutting and marking technology into the manufacturing process adds another dimension of efficiency and speed to the industries.One firm that has embraced laser technology is a global leader in vacuum equipment production. They recently added two new laser machines to their production line, a fiber and a CO2 laser. By combining these two types of lasers, the company has been able to achieve a higher degree of precision, speed, and flexibility, helping them meet the growing demands of their customer base.Incorporating these high-tech lasers has already led to significant improvements in one of their key products, vacuum flanges. The CO2 laser, which is particularly suited for engraving, has allowed the company to add product identification and branding into their flanges, improving customer recognition and product support. The fiber laser, on the other hand, has enabled the firm to cut and weld thin materials with incredible accuracy, resulting in high-quality flanges and increased efficiency in the manufacturing process.The decision to integrate fiber and CO2 lasers is part of a broader plan by the vacuum equipment manufacturer to modernize their manufacturing process. By investing in cutting-edge technology such as lasers, they are staying ahead of the curve and providing their customers with high-quality products.One of the key advantages of laser technology is that it is easily automatable, which can help manufacturers save valuable time and money. For the vacuum equipment producer, automating their manufacturing process has allowed them to increase production while reducing labor costs.Another benefit of using lasers is the reduction in waste, particularly when cutting materials. Lasers produce a clean, precise cut, resulting in less wastage and a lower environmental footprint.The addition of fiber and CO2 lasers to their production line has also helped the vacuum equipment manufacturer to stay ahead of their competitors. By investing in technology that allows them to improve product quality and efficiency, they are better positioned to meet the needs of their customers and remain competitive in their market.In conclusion, the integration of laser technology into manufacturing processes has revolutionized many industries in recent years, and its impact is only set to increase in the future. Fiber and CO2 lasers are particularly versatile and allow businesses to achieve a higher degree of precision and efficiency in their operations. By investing in laser technology, the vacuum equipment manufacturer has been able to achieve significant improvements in their manufacturing processes, including increased production, reduced waste, and higher-quality products. With technology advancements by the day, machine automation will further increase precision and speed in manufacturing processes.
Efficient Factory for Blade Cleaning: Revolutionizing the Industry
Blade Cleaner Factory, a leading manufacturer in the cleaning industry, has announced its plans to revolutionize the way blades are cleaned with its innovative solution. Leveraging years of expertise and technological advancements, the company aims to provide efficient, safe, and environmentally friendly cleaning methods for various industries.With a commitment to surpassing customer expectations, Blade Cleaner Factory offers a diverse range of cleaning solutions tailored to specific industries' needs. From the food and beverage sector to medical and surgical instruments, the company ensures superior cleaning results in a cost-effective manner.Blade Cleaner Factory's state-of-the-art machinery and equipment guarantee the removal of contaminants, residue, and debris from blades, improving efficiency and extending lifespan. By incorporating cutting-edge technology, such as ultrasonic cleaning and high-pressure water jets, their solutions deliver optimum cleanliness while preventing any damage to the blades.The company's core values of innovation, quality, and sustainability shine through in its commitment to reducing environmental impact. Blade Cleaner Factory utilizes eco-friendly cleaning agents and techniques that comply with stringent regulations while delivering exceptional results. Customers can rely on the company's expertise to not only achieve cleanliness standards but also minimize their carbon footprint."We understand the importance of not only providing effective cleaning solutions but also doing so in an environmentally responsible manner," said the company spokesperson. "Our team continuously works on improving our processes and investing in sustainable technologies that align with our commitment to the planet."Blade Cleaner Factory's dedication to customer satisfaction extends beyond the quality of their products. The company offers comprehensive after-sales support and maintenance services to ensure continued efficiency and longevity of their cleaning solutions. A team of highly skilled technicians is available for on-site assistance, maintenance, and training, providing customers with peace of mind and minimizing downtime."Our aim is to establish long-term partnerships with our clients. We believe that by providing reliable products and exceptional support, we can contribute to their success," added the spokesperson. "We go the extra mile to understand our customers' unique requirements and offer customized solutions that address their specific challenges."Blade Cleaner Factory's commitment to excellence has earned them a stellar reputation in the industry. Their client portfolio includes major players in various sectors, including food processing plants, hospitals, and laboratories. The company's dedication to continuous improvement and innovation has set them apart, making them the top choice for blade cleaning solutions.As the cleaning industry continues to evolve, Blade Cleaner Factory remains at the forefront with its cutting-edge technologies and customer-centric approach. With a strong emphasis on sustainability, they are poised to lead the way in providing efficient and environmentally friendly cleaning solutions.About Blade Cleaner Factory:Blade Cleaner Factory is a global manufacturer specializing in innovative blade cleaning solutions. With a focus on quality, reliability, and sustainability, they offer a comprehensive range of cleaning equipment to various industries. Through continuous innovation and unparalleled customer support, Blade Cleaner Factory strives to be the leader in the cleaning industry, setting new standards for efficiency and environmental responsibility.
New Smart Factory Increases Production Capacity by 30% with Automated Equipment
DFI's New Smart Factory Brings Innovation to Industrial ComputingDFI, the world's leading brand in embedded motherboards and industrial computers, recently unveiled their new smart factory. The factory is packed with cutting-edge automated equipment, and the company believes this will improve their production capacity by up to 30%.The new smart factory, located in Taiwan, includes a range of cutting-edge automated equipment. These include advanced machines for cutting, drilling, milling, assembly, testing, and packaging. The company says that these innovations will improve both quality and efficiency.According to DFI spokespersons, the company has designed the smart factory to be flexible, scalable, and sustainable. For instance, the factory boasts modular designs that enable fast reconfigurations and easy upgrades. The factory is also equipped with advanced sensors that can monitor critical factors such as temperature, humidity, energy usage, and safety.DFI's smart factory is capable of processing orders promptly and efficiently. The factory has an automatic material handling system that simplifies the movement of goods throughout the production process. The production line can also produce customized orders with minimal changeover times.DFI believes that with the new smart factory, they will enhance the quality of their products while maintaining the highest standards of safety and sustainability. The company has achieved this by incorporating Industry 4.0 principles, which focus on interconnecting machines, digitization, and data analytics.The introduction of the smart factory is good news for DFI's customers. The factory will give the company the ability to produce more robust and reliable embedded motherboards and industrial computers. This, in turn, will help customers who rely on DFI's products for their operations.DFI's new smart factory also improves its competitiveness in the global market. As a leader in industrial computing, DFI's products are used in various sectors, including healthcare, transportation, automation, and manufacturing. With the smart factory, DFI can increase its production capacity and process orders more quickly.The smart factory will also boost DFI's sustainability efforts. Automated equipment will reduce the use of manual labor, minimizing the factory's carbon footprint. Furthermore, the factory's sensors will allow the company to monitor energy usage and optimize efficiency without compromising quality.During the factory's inauguration, DFI invited the media to tour the facility. Reporters were able to witness the factory's advanced equipment and the company's dedication to advancing computing technologies. The attendees were impressed by the new facility and the cutting-edge technologies that it integrated.In conclusion, DFI's new smart factory is a significant milestone for the company. With state-of-the-art automated equipment, DFI can produce more robust and reliable embedded motherboards and industrial computers. The smart factory will improve the quality and efficiency of DFI's production process, and enhance the company's competitiveness in the global market. Moreover, the factory's sustainability features align with DFI's commitment to environmental responsibility and social progress.
Cutting Metal Processing Technology with CNC Machine - Stock Video
Machines.Laser Cutting: Advanced Metal Cutting TechnologyLaser cutting is an advanced metal cutting technology that has revolutionized various manufacturing industries. This technology has enabled manufacturers to create precise, intricate designs in a wide range of materials. Since its inception, laser cutting has become an essential process for many applications such as automotive, aerospace, defense, electronics, and medical devices.One of the major reasons why laser cutting is so popular is the precision it offers. Laser cutting machines use a high-powered laser beam to cut through metal with incredible accuracy. This allows manufacturers to create complex, intricate designs that can not be replicated using traditional cutting methods. The laser beam can also work with a range of materials including metals, plastics, wood, and ceramics.CNC Machines and Laser CuttingComputer Numerical Control (CNC) machines are a critical component of laser cutting technology. These machines are programmed to operate the laser cutter using pre-set parameters. CNC machines and laser cutting are highly compatible because they allow for detailed and accurate designs to be created in a short amount of time.CNC machines also allow for the creation of reproducible parts that are identical, regardless of the number of times they are produced. This makes the manufacturing process much more efficient, saving time and money in the long run.Metal Cutting with Laser CNC MachinesLaser cutting technology has significantly revolutionized the metal cutting process. Metal cutting with laser CNC machines offers a lot of advantages to manufacturers. Firstly, the cutting process is quicker and more precise compared to traditional cutting methods. Secondly, laser cutting does not produce any burrs or chips, making it ideal for high-precision applications. Thirdly, laser cutting provides superior edge quality with less surface contamination. As a result, finished products have a cleaner and smoother finish.ConclusionMetal cutting with laser CNC machines is an excellent example of how technology continues to positively impact manufacturing processes. By utilizing advanced laser cutting technology, manufacturers can achieve high-precision results, creating intricate designs, and reducing production time and cost. With CNC machines and laser cutting, reproducibility and consistency are also ensured, thereby enhancing the overall efficiency of the production process. By adopting this technology, manufacturers can deliver high-quality products that meet the strictest customer requirements.
Powerful Handheld Laser Welding Machine for 3.0mm Stainless Steel Applications
In recent times, the laser welding industry has undergone a significant change, with the proliferation of handheld laser welding machines. Handheld laser welding machine is an extremely efficient tool that offers significant advantages in terms of precision, cost-effectiveness, and versatility. Dapeng Laser Home, a leading company in China, has introduced a 1500 watt handheld laser welding machine.The new 1500 watt handheld laser welding machine is a breakthrough innovation that is capable of welding 3.0 mm stainless steel with ease. The product is designed to be user-friendly and efficient with a compact design that makes it portable and easy to carry around. The welding machine is equipped with advanced technology that reduces welding time, making it ideal for industrial and commercial applications.The machine's high power output and high-speed laser beam enable it to carry out various welding tasks, including spot welding, seam welding, and welding of thin plates, pipes, and tubes. Its excellent beam quality and precision welding make it an excellent choice for any welding project.Dapeng Laser Home, with over ten years of experience in the laser industry, has produced an amazing innovation that has won the hearts of welding professionals in China and worldwide. The company has been at the forefront of the laser industry, providing high-quality products that meet the growing demand for advanced welding solutions. The 1500 watt handheld laser welding machine is an example of the company's commitment to producing innovative laser products that meet the evolving needs of the industry.According to the company, the machine guarantees up to 95% welding rate, ensuring a high-quality weld that is consistent throughout the welding process. It also guarantees energy conservation, ensuring that users minimize their carbon footprint while also reducing energy costs. The machine is also equipped with an automatic alarm system that warns the operator of any abnormalities during the welding process, increasing safety while using the machine.Aside from the machine's high precision welding ability, it also boasts low maintenance costs and high durability. With the machine, users can expect reduced downtime, increased efficiency, and enhanced productivity. The machine is easy to operate, not requiring extensive training, which reduces frustration and gets you up and running in no time.Dapeng Laser Home has positioned itself at the forefront of the laser industry with the introduction of this 1500 watt handheld laser welding machine. The machine's high power output, excellent beam quality, precision, and user-friendly design have made it a favorite among welding professionals worldwide. The company's commitment to producing high-quality products has won it many clients in China and beyond.In conclusion, the 1500 watt handheld laser welding machine is an excellent choice for anyone seeking a versatile, cost-effective, and precise welding solution. With its high speed, precision welding, reduced downtime, and low maintenance cost, the machine is a valuable tool in the welding industry. Dapeng Laser Home has produced an innovation that is making a significant impact in the industry, and with its commitment to continual improvement, the company's future looks bright.